Masterstudio; Architect changemaker sem 01
Anna Eppelmann

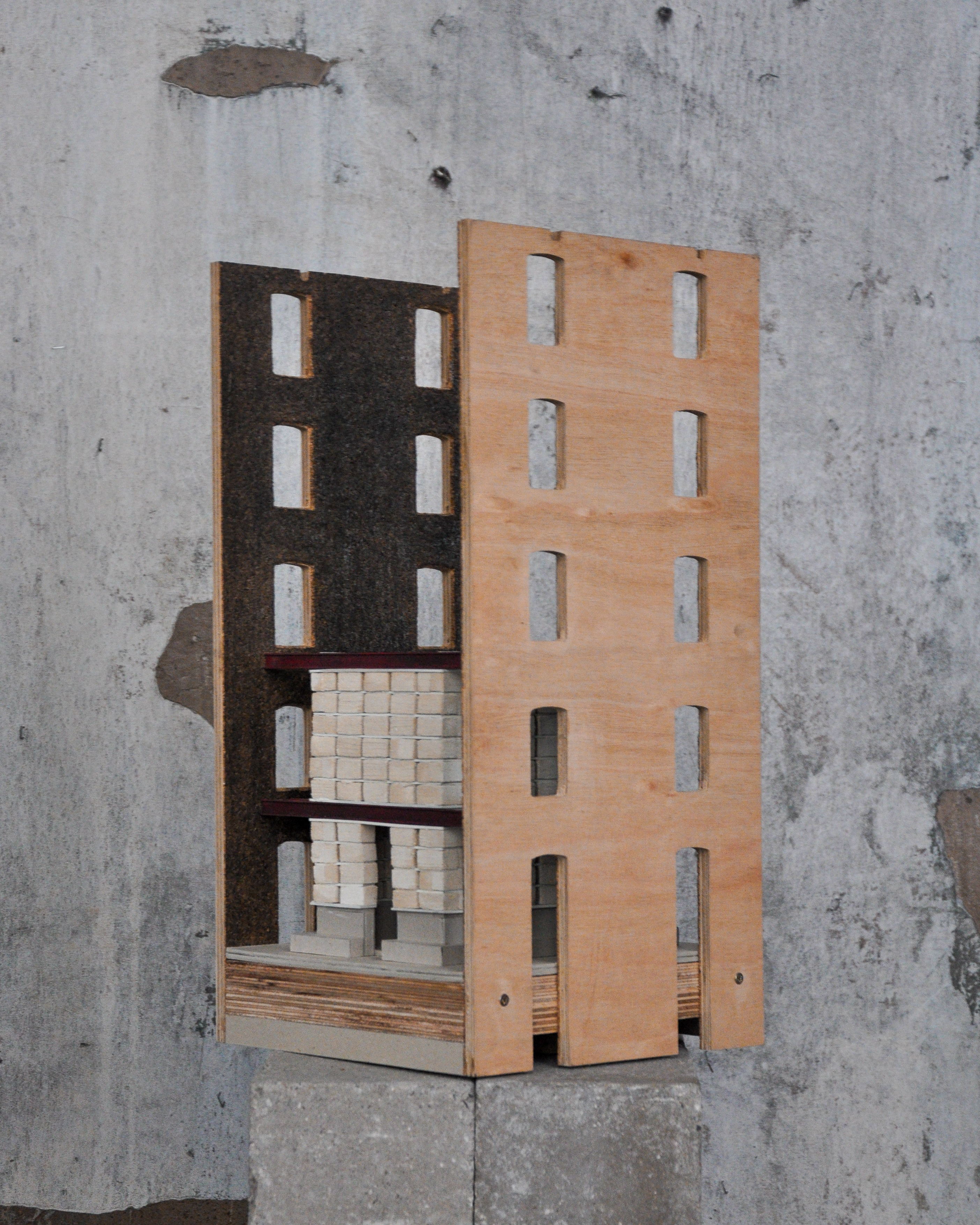

Sheep's wool has become a waste product in recent years for various reasons. In Belgium, sheep are mainly kept for meat and milk production. However, due to their high quality and strong competition, their wool no longer finds a buyer on the global wool market. Farmers store the wool
for years without using it or desperately try to burn it.
This structure uses it as a valuable resource and is built 100% out of wool, pushing this material to its limits. It is largely determined by the special properties of wool. The scale-like fiber structure enables matting through mechanical action, moist and heat. It creates a product that is equallystrong in all directions and very light in relation to it’s density and tensile strength.
The design is intended to create a place of contemplation and rest, benefitting from the insulating, moisture-regulating, acoustically dampening and soft properties of wool. The outer structure therefore distances itself from the rough existing building and contrasts it. The self-supporting
structure is created out of felted blocks and boards in different densities and an inner wool lining that only allows filtered light to pass through. This is achieved by pre-compressing and de-compressing the modules between the existing I-Beam structure and a felted support structure.
Due to the different densities and the compression, the blocks form a stable wall. The inner structure is intended to create further spaces and possibilities for resting: smaller and bigger,darker and lighter. Therefore a ladder leads to the inner core of combed and stacked wool, that is built in the same principle. The floor itself is out of dense wool felt, that is not only self load-bearing but can also carry a person.
The idea for the implementation is that the tannery in Vironvail could serve as a collection point for the wool waste of the area. The existing infrastructure in Verviers could be used for further processing. There, the wool can be washed in the only wool washing plant and processed into felts in the surrounding factories. The finished parts are then delivered to the construction site and only need to be assembled. This is effective, time and energy saving compared to other options.
To close the material cycle, the parts of the pavilion can easily be deconstructed. The modulescan be reused, recycled or composted.